
A worker assembles Volkswagen electric cars at the company’s plant in Zwickau, Germany on Jan. 27. Automakers like Volkswagen are racing to secure enough metals to power the batteries needed to make electric vehicles.
Jens Schlueter/Getty Images
hide caption
toggle caption
Jens Schlueter/Getty Images
A worker assembles Volkswagen electric cars at the company’s plant in Zwickau, Germany on Jan. 27. Automakers like Volkswagen are racing to secure enough metals to power the batteries needed to make electric vehicles.
Jens Schlueter/Getty Images
As automakers race to go electric, there’s a big problem lurking underground.
Companies are betting hundreds of billions of dollars on electric cars and trucks. To make them, they’ll need a lot of batteries. And that means they need a lot of minerals, like lithium, cobalt and nickel, to be dug up out of the earth.
These minerals aren’t particularly rare, but production needs to scale up massively — at an unprecedented pace — to meet the auto industry’s ambitions.
And there’s another big challenge: The existing supply chain is dominated by a single country: China.
“China pretty much controls almost all the metals required,” says Kwasi Ampofo, the head of metals and mining at the research company BloombergNEF.
It’s not just profits on the line. Climate experts say the world needs to phase out gasoline-powered vehicles quickly to limit the worst effects of climate change.
The urgent need to access these minerals has industries and governments alike rethinking their entire approach to supply chains.
How a handful of metals could determine the future of the electric car industry
China’s dominance raises big geopolitical concerns
Beijing controls about three-quarters of the market for the minerals that are essential for batteries.
It’s not that China won the geological lottery and just happened to have really rich deposits of these minerals. In fact, the richest deposits are in places like the Democratic Republic of the Congo, Australia and Chile.
But China set out intentionally to dominate the processing of these minerals, as part of a plan to become a major player in electric vehicles.
Beijing had the authoritarian power, the money, the massive market and the will to make that happen. And it worked — much to the anxiety of the West.
“We like to say we’re in competition with China, but it verges on to the point of conflict,” says Mary Lovely, a senior fellow at the Peterson Institute for International Economics.
Meanwhile, the war in Ukraine has created a new kind of anxiety. Russia, while a much smaller player than China in these supply chains, provides a significant amount of nickel in global markets, which has sent prices of the mineral soaring since the invasion began.
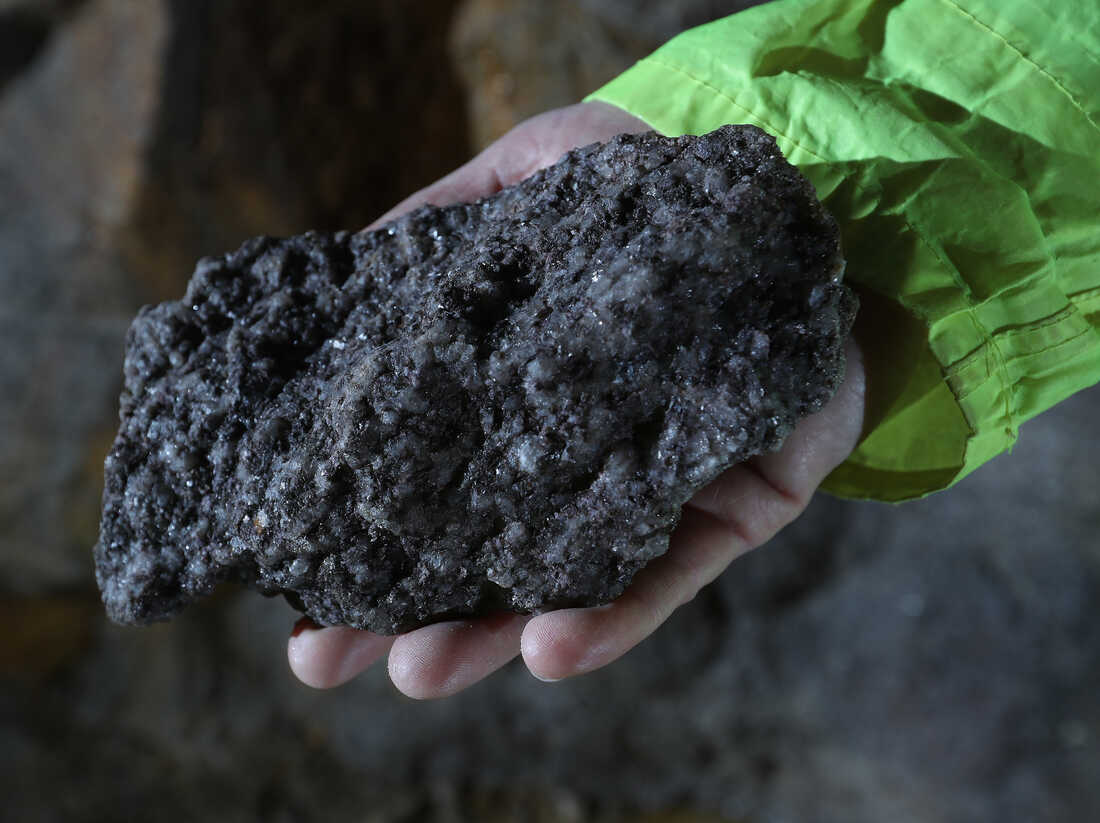
A rock of Zinnwaldite, a silicate mineral that contains lithium, from a mine near Altenberg, Germany, is shown on Dec. 13, 2017.
Sean Gallup/Getty Images
hide caption
toggle caption
Sean Gallup/Getty Images
A rock of Zinnwaldite, a silicate mineral that contains lithium, from a mine near Altenberg, Germany, is shown on Dec. 13, 2017.
Sean Gallup/Getty Images
The U.S. wants to reduce its reliance on China
Worried about future access to battery minerals, the Biden administration and other governments around the world are trying to build up their domestic supply chains to reduce their dependence on China.
Congress has earmarked $3 billion to support U.S.-based mining and processing of battery minerals. Companies are racing to get projects off the ground — or rather, into the ground.
But in the U.S., many communities are understandably reluctant to allow a new mine or refinery to open.
Trent Mell is the CEO of Electra, a company working to process cobalt in Canada. He points out that Idaho has significant cobalt deposits — mostly on U.S. Forest Service land. It’s not easy to get permission to mine there.
“I’ve been a miner for 20 years,” Mell says. “America is one of the best places in the world to mine, but one of the harder places in the Western world to permit.”
And even a successful effort to launch new mining and refining capacity will take time.
“China saw the vision 10 years ago, and then it took … almost a decade for the fruits to start bearing,” Ampofo says. “There’s no short-term fix here.”
How a handful of metals could determine the future of the electric car industry
Auto industry rethinks its supply chains
Meanwhile, automakers aren’t just concerned about the geopolitical risks of their current supply chain. They’re also deeply worried about the sheer volume of minerals they’ll need.
Demand for some mined products could scale up tenfold within a handful of years.
“You can’t just go in and secure supply because it doesn’t exist for the future. It has to be built,” says Eric Norris, the president of the lithium business at Albermarle Corporation, a U.S.-based company that is a major lithium producer.
So companies like General Motors, Volkswagen and BMW are making the very unusual move of purchasing minerals directly from mines — and in some cases, even investing in them, to make sure they have the resources they need to scale up.
This is a major shift for automakers who typically rely on a network of suppliers who deliver the parts and components they need exactly when they want them. That’s like buying ice cream from the store today, because you want it now.
Developing their own direct sourcing of minerals, on the other hand, is like calling a farmer to reserve a cow so you can have milk for ice cream next year.
Tesla, the revolutionary electric automaker, has been calling mines directly for years.
“It was a matter of survival,” says Vivas Kumar, who used to work at Tesla sourcing battery materials and now runs a battery component startup.
Now, other automakers see it the same way.
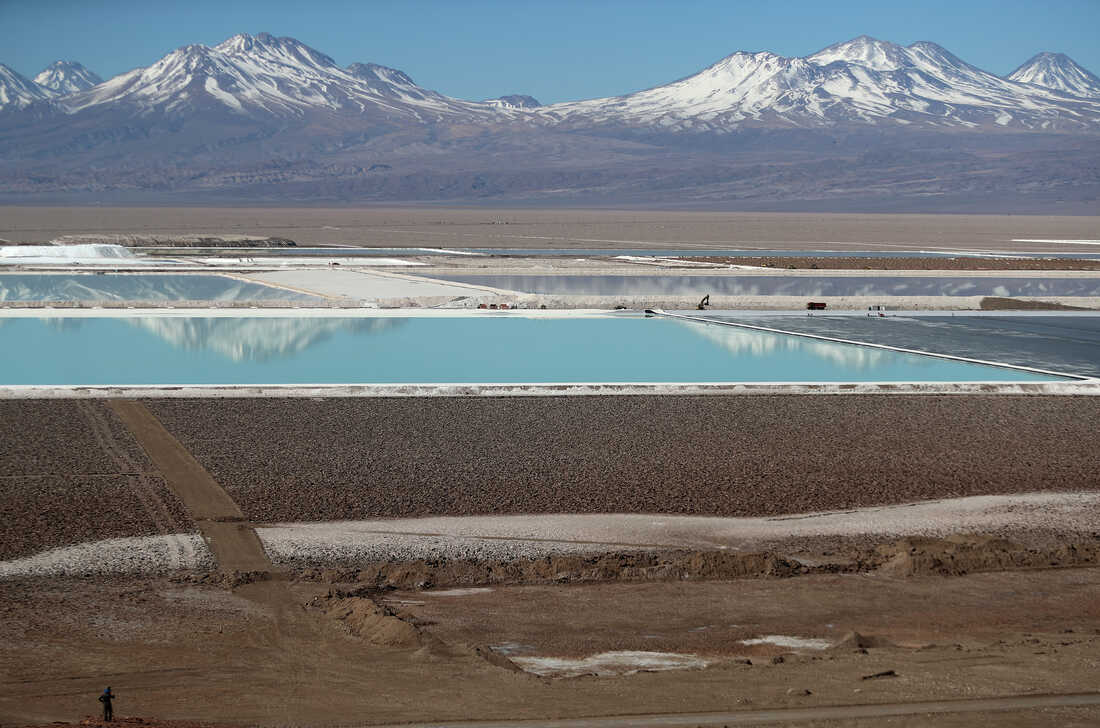
Brine pools from a lithium mine owned by U.S.-based Albemarle Corporation are seen in the Atacama desert, Chile, on Aug. 16, 2018. Mines like these are the start of a global supply chain for battery materials that has become critically important as electric vehicles rise in popularity.
Ivan Alvarado/Reuters
hide caption
toggle caption
Ivan Alvarado/Reuters
Brine pools from a lithium mine owned by U.S.-based Albemarle Corporation are seen in the Atacama desert, Chile, on Aug. 16, 2018. Mines like these are the start of a global supply chain for battery materials that has become critically important as electric vehicles rise in popularity.
Ivan Alvarado/Reuters
The global mining industry could also be impacted
The push to secure minerals for batteries could have ramifications beyond the auto industry.
For one thing, it could put pressure on the mining industry to improve its practices. The industry’s checkered history includes using child labor at cobalt mines in the Congo, and causing pollution and deadly accidents at mines and refineries around the world.
When a mine sells their products into a long, convoluted supply chain, an individual mine is essentially immune to boycotts or public pressure.
Automakers, on the other hand, care a lot what the public thinks of them – and especially what they think about their eco-friendly-branded electric vehicles. That means deals directly between carmakers and mines come with pressure to avoid disasters and abuses.
“When the auto sector came in, they changed everything,” says Aimee Boulanger, the executive director of the Initiative for Responsible Mining Assurance.
She says mines that brushed off ethical concerns from other buyers are paying attention to automakers’ demands, because of the mind-boggling quantities of minerals the global carmakers are about to buy. It’s no substitute for adequate regulation, she says, but it’s already having an impact.

Can automakers get it right?
For automakers, meanwhile, the stakes couldn’t be higher as they race to secure the minerals they’ll need to pivot to an electric future.
The shortage of semiconductors that has halted production lines around the globe is an example of how critical it is for automakers to get their supply chains right.
Scott Keogh, the CEO of Volkswagen of America, calls the scaling up of the battery supply chain a “high-wire act.”
But Keogh is confident.
“You have some of the world’s largest amount of capital, some of the world’s best mines, all of the major governments and major industries attacking this issue from all fronts,” he says. “I have a lot of confidence we can solve it.”
They have to.
Eight years from now, he’s expecting fully half of VW’s production to be battery-powered vehicles.